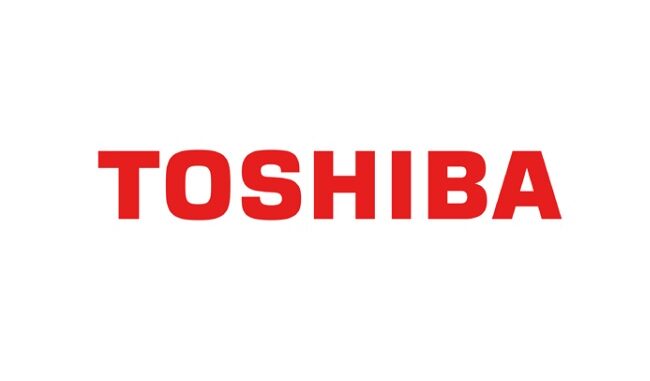
東芝は10月17日、深層学習を使って、技術者のプログラミングが不要で、複数の吸着パッドを持つロボットハンドが、物流現場で対象物の形状に合わせて把持する動作を正確で高速に計算可能なAI(人工知能)技術を開発したと発表した。
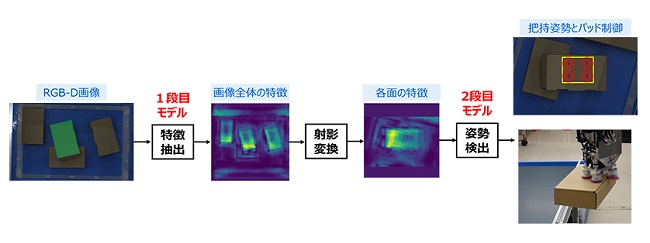
開発した手法は、ロボットハンドが対象物に接触できる面を検出する1段目のモデルと、検出した面の法線方向に基づいて射影変換させた画像からハンドの向きと吸着位置を決定する2段目のモデルで構成。
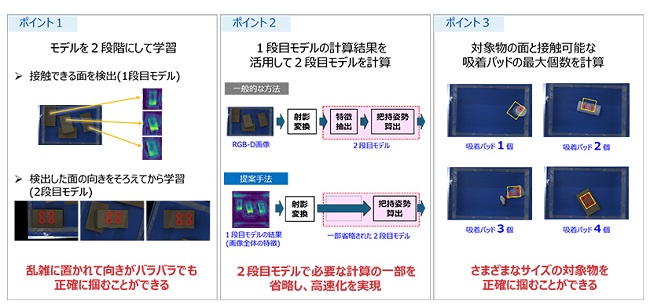
1段目のモデルで出力される情報(特徴マップ)を2段目のモデルの計算にも活用することで、繰り返しの計算を不要にすると共に、一回で把持可能な吸着位置を特定できるようになり、計算時間を大幅に短縮した。
従来手法では、対象物を画像として写し、吸着パッドの吸着候補位置を推定する計算を繰り返し行い、その中からベストな把持位置を決定していたため、吸着位置の計算に時間がかかっていた。
東芝によると、従来技術は対象物が密集している場合に精度が低下する傾向があったが、今回、独自技術で、対象物の傾きに合わせて、ロボットハンドの姿勢の正確な学習が行えるようにすることで、物体の向きがバラバラで乱雑に置かれていても把持を可能にした。
同社は、開発したAIに実際のロボットに搭載したカメラから取得した画像約4000枚を事前学習させて、272枚の画像を対象に把持位置の計算時間と精度の検証を実施。
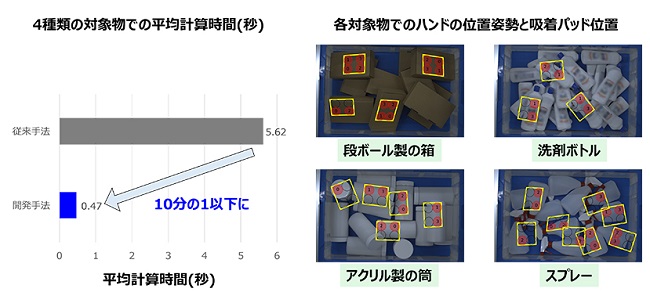
その結果、同様の先行研究例の計算時間5.62秒、成功率73.9%と比較し、計算時間は0.47秒と10分の1以下、成功率は6.2%アップの80.1%と、世界最高の平均計算速度と平均成功率の達成を確かめた。また、AIを実機ロボットに適用したところ、94.5%の平均成功率で対象物を把持ができ、実用化レベルであることも確認した。
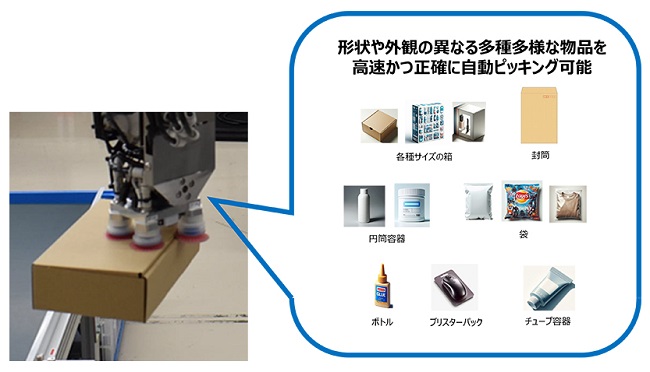
東芝では、検証結果を受け、AIで封筒や書類などの平面の物品から、異なるサイズの箱、円筒容器、チューブ容器、ブリスターパックなどの高さや奥行き、凹凸のある物品など、形状や外観の異なる多種多様な物品をロボットハンドで高速で正確に自動でピッキングが可能になるとしている。
また、AIの学習は技術者のプログラミングが不要なため、ロボット導入後に対象物の種類が増えた場合でも追加学習が容易に行えるため、ロボット全体のコストを低減できるという。
ロボットハンドは4つの吸着パッドを搭載し、それぞれのパッドを個別に制御することが可能。吸着パッドをいくつ使うか、どれを使うかといった計算を対象物のサイズや形状に合わせて行うことができる。今後は実際の物流倉庫での実証と研究開発を進め、2026年度以降に開発したAIを搭載した製品の実用化を目指す。