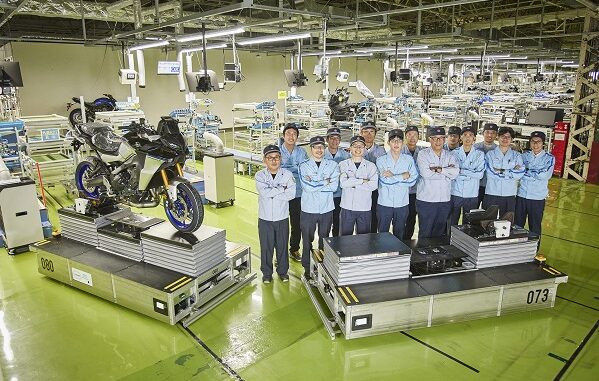
ヤマハ発動機は、静岡県磐田市の本社オートバイ組み立て工場にAGV(無人搬送車)を活用した生産システムを導入し、今春から本格的な稼働を開始した。
オートバイは「実は季節商品。需要変動に合わせてたくさんの種類を少しずつ生産する『多品種少量生産』という難しさがある」(組み立て技術部の曽貝健司氏)。実際、本社オートバイ組み立て工場で扱う部品の点数は、1日あたり約9000種、合計60万点にも上る。「同じものを常に同じ量を作るのであれば設備や仕組みをもっとシンプルにすることも可能だが、そうはいかない」(同)という。
そのため、従来のコンベア方式では「需要変動で、あるラインでは昼夜問わずフル稼働する一方、隣のラインは休眠中という非効率な状況が生まれていた。作業者にとっても変化が大きく、働きやすい職場ではなかった」(同)。そこで、ヤマハでは、この課題の解決で、AVGを使った新たな生産システム「AGVバイパス方式」を開発した。
AGVで多品種少量生産に対応
AGVバイパス方式は、135台の特殊なAGVを使用する。具体的には、作業台を載せたAGVが複数連結することで組み立てラインを形成。AGVは、時には列を成し、時には列から外れて工場内を走行する。それは「例えば、複数のモデルを同時に流す場合、各工程で組み付ける部品点数や作業時間がそれぞれ異なる」と、システムを開発した小林篤史氏は説明する。
システムの名称については「前に並ぶ製品の工程に時間を要する時や、その工程自体が不要な場合に、後ろに並ぶAGVがラインを外れて、定められた次の工程に自ら移動する。そして、渋滞路を外れて目的地まで直行するという意味で、『バイパス方式』と呼んでいる」(小林氏)と話す。
AGVがモノと働く人の情報を携え工場内を移動
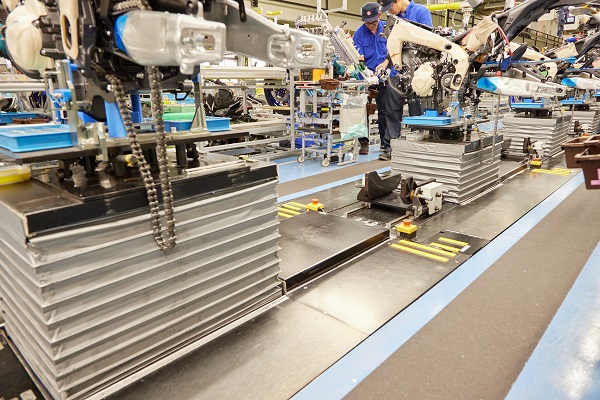
AGVバイパス方式では、車両を載せたAGVが、各製品、各工程、各作業者の情報を携えて移動。AVGは、向かった先々のツールや設備に組み立て情報の指示を出し、作業者の身長や作業部位でリフトの高さを最適化する。この仕組みによって、突然舞い込んでくる1台の生産要請にも応える対応力と汎用性を実現。その結果、「多品種少量生産」という長年の課題解消につながった。
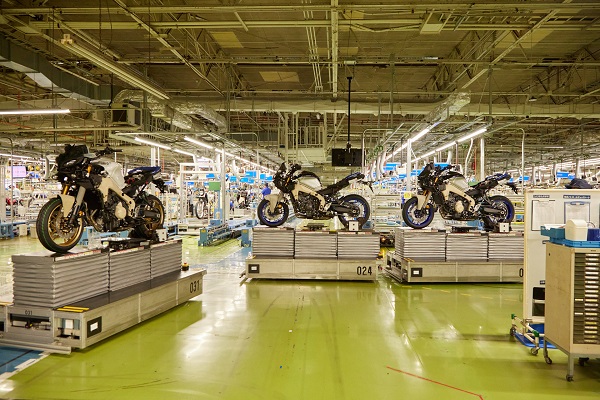
「『AGVバイパス方式」は、生産の効率化だけでなく、働き方改革や省エネなどにも効果を発揮している。今後、EV(電気自動車)化を始め、モノづくりの多様化にも柔軟に対応する仕組みとして作り上げた」と、曽貝氏は話す。
AGVバイパス方式の導入で、5年ほど前には8本あった常設の車体組み立てラインは現在では4本までに半減した。ヤマハでは新たな技術で、人がいきいきと働くことができる製造を自動化する「スマートファクトリー」を実現し、組み立て工場の革新を目指している。